今月末には販売開始予定の、市販キャブ用バキュームニップル付インシュレーター
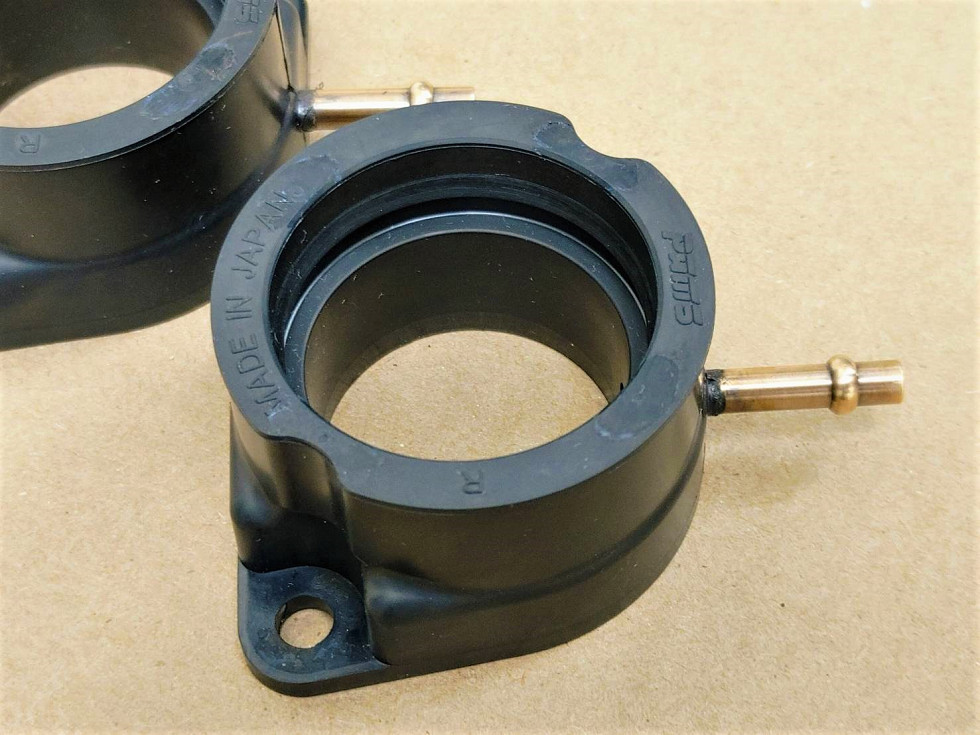
純正のZ1000J系用の代替品としてでは無く、ゴムの品質や各部寸法も練り直して上回るものをと製作してきましたが、何よりの特徴はやはり社外キャブ使用時にスロットル同調を取る為のバキュームニップルの装備です。
インシュレーター側にこのニップルを位置すると、キャブレターのスピゴットを長く取る必要は無くなります。
このニップルパイプは、インシュレーターのゴムを加硫成型する際に金型に組み込んで同時に焼き付けしています。
これによるゴムに対する密着は、一般の接着等によるものより遥かに強力です。
例えばですが、このパイプ。固定が甘い場合はバキュームゲージに繋げたホースを取り外す際には一緒に引き抜けてしまいますし、逆に作業後にキャップを取り付けする際には中に潜り込んでしまって用を足さないでしょう。
又、抜けてしまうならまだしも、内側に押し込まれた場合はエンジン内部に吸い込まれてしまう可能性も高く、その場合は燃焼室やピストン,バルブ等を破損させて深刻なダメージを発生する事になります。
通常のオーバーホールではきかないレベルでの修理コストが発生する可能性があり、あまりにも大きなリスクになります。
この為完成インシュレーターへのニップルパイプ後組み込みの考えはかなり早くに除外して、金型コストは大幅に増大するのですが純正のZ1用その他のもの同様に同時に加硫成型して焼き付けの方法を採りました。
さて、加硫による接着がどの程度の強度を持つかです。
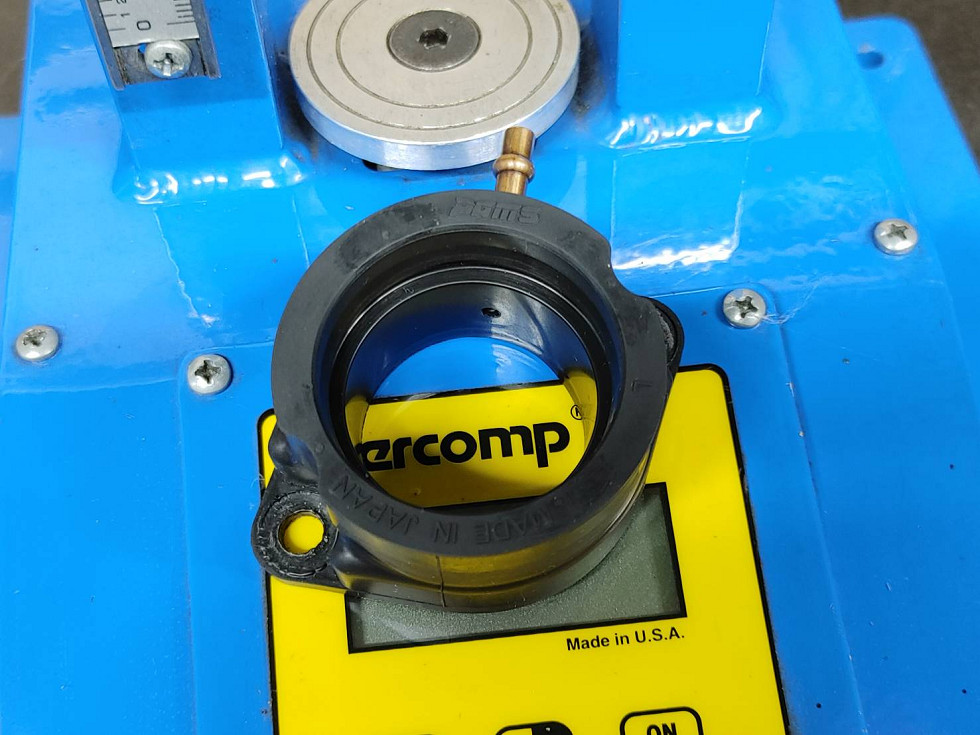
荷重を測定しながらかけるのに、バルブスプリングテスターを使います。
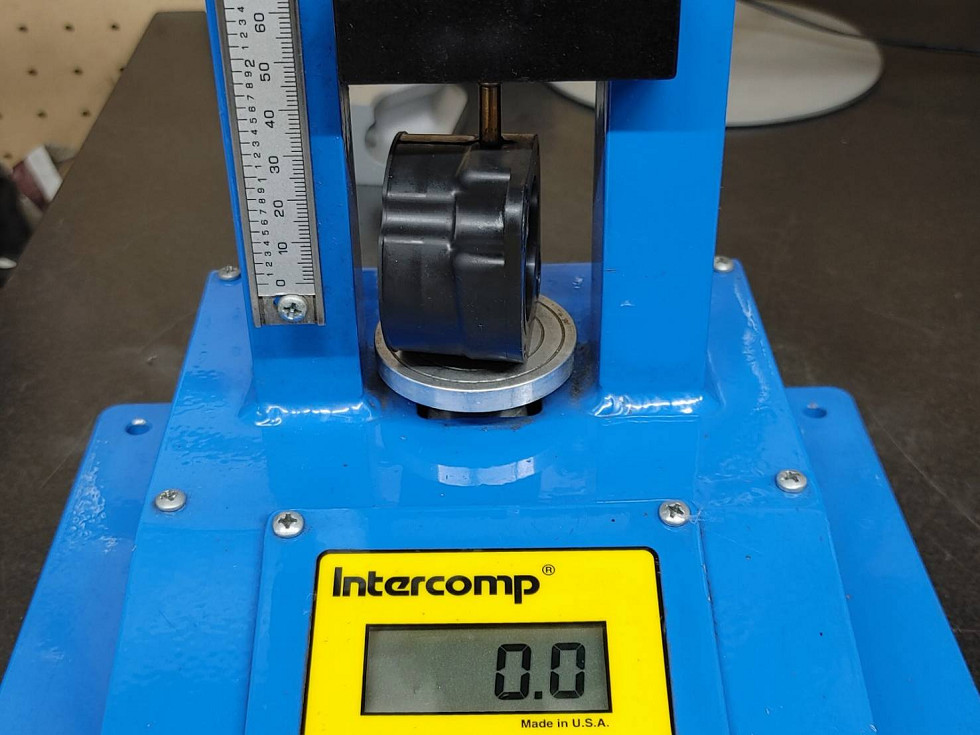
パイプに直接押し込みする為の力をかけます。
インシュレーター全体は合成ゴム製ですが、内部に鉄板が入っていますので、潰れません。
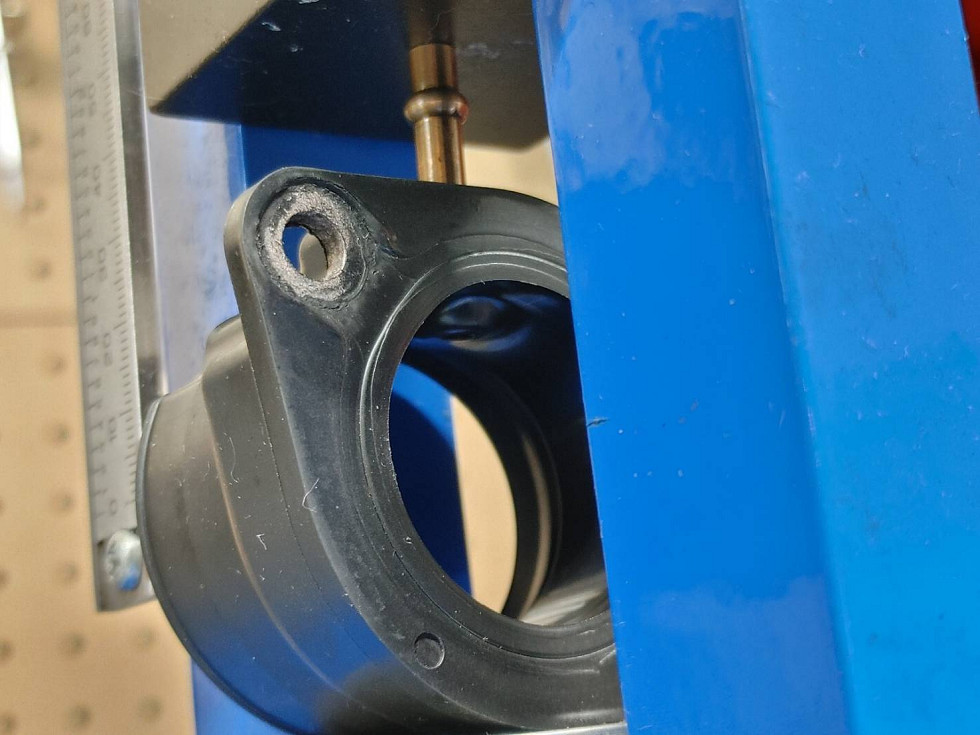
30㎏かかってパイプが押し込まれています。
ホースやキャップの脱着と言った通常の使用でこれ程の力がパイプ部のみにかかる事はまず考えられません。
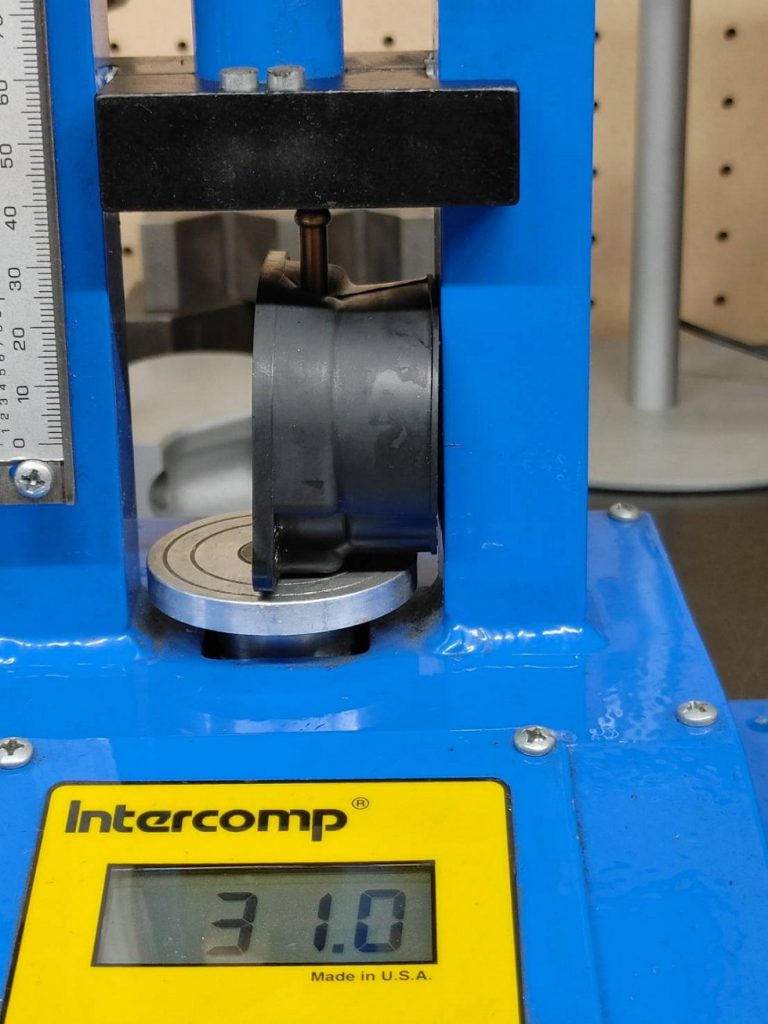
パイプが周辺のゴムを引っ張りながら押し込まれています。
ちなみにこのインシュレーターは加硫成型した新品では無く、先行テストで使用して内部にガソリンが通り続けたものを使用しています。
より現実の使用条件に近づける為です。
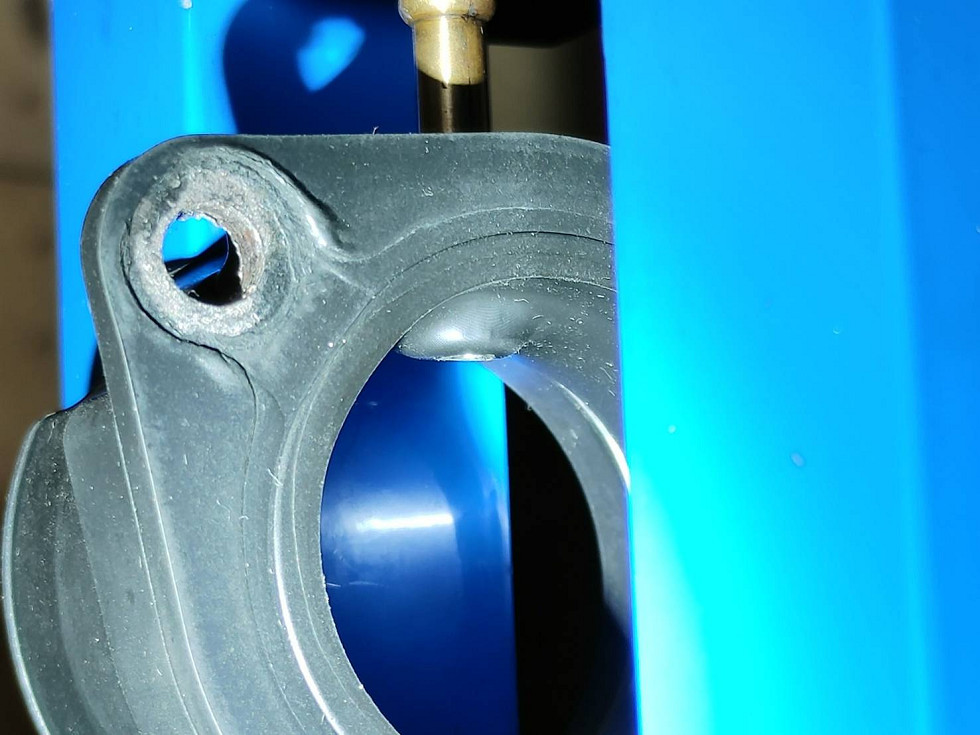
荷重を抜いては再度30㎏をかけてと、数十回繰り返します。
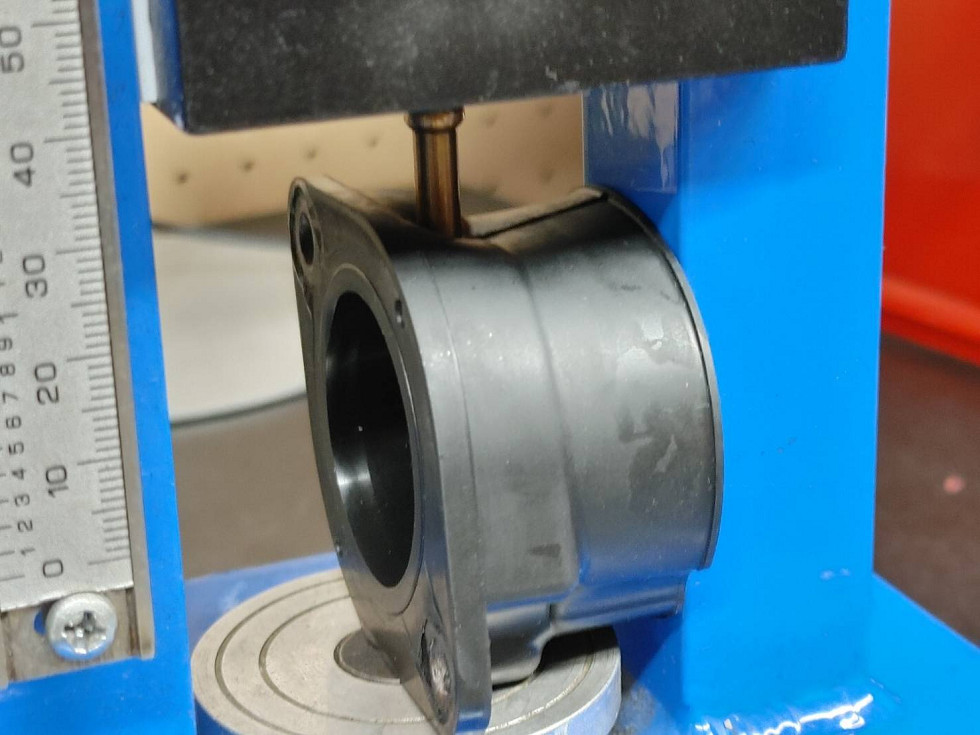
結果として、パイプ周囲は荷重がかかった時は変型こそすれど荷重が抜ければ元通りになり、ゴムから剥離してしまう様な事はありません。
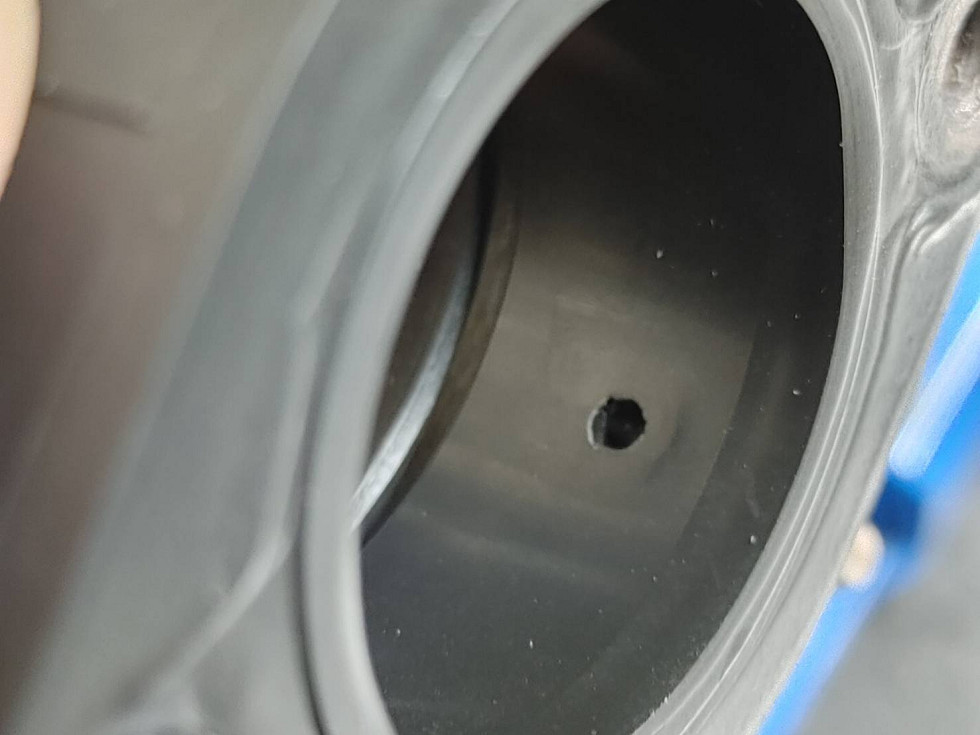
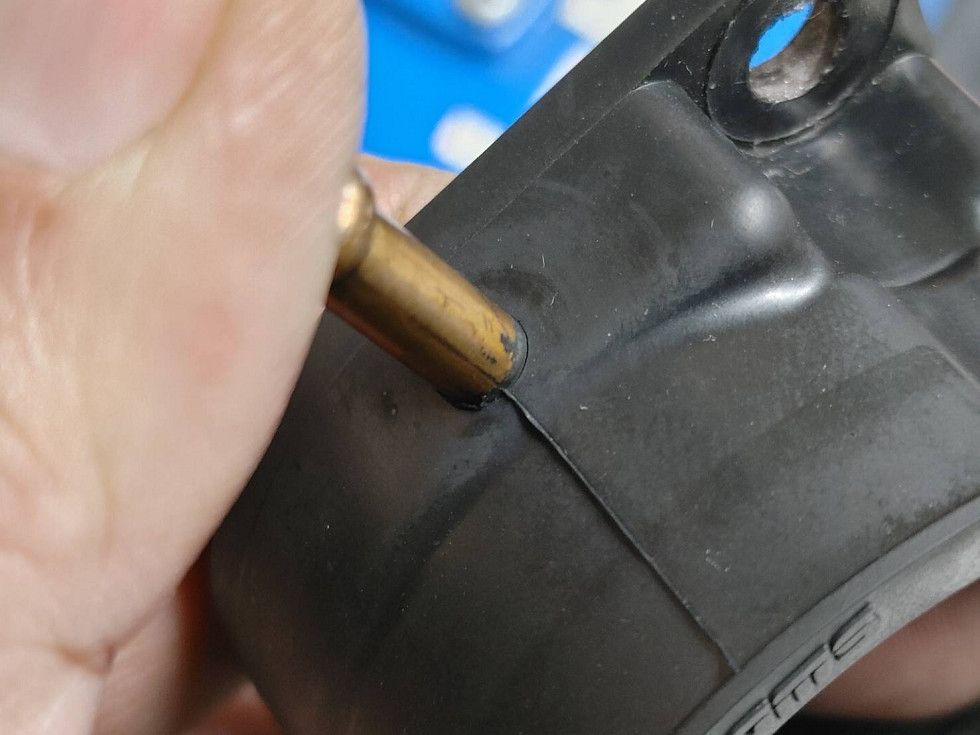
耐久テストとしては、実際に壊れる迄行って限界を知るのが正しいです。
段階を追って荷重を増やします。
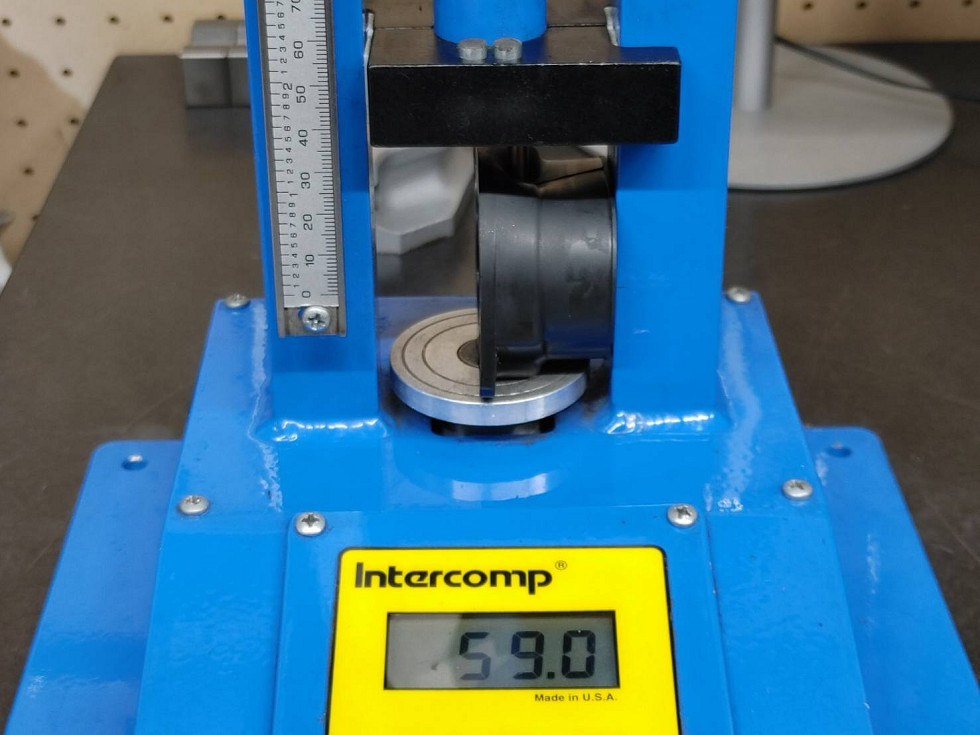
60㎏を超えたあたりで、変形した内側に亀裂が入り始めました。
そのまま押し込んでいくとインシュレーターが裂けました。
この細いパイプに人間一人分の荷重をかけないと壊れない事になります。
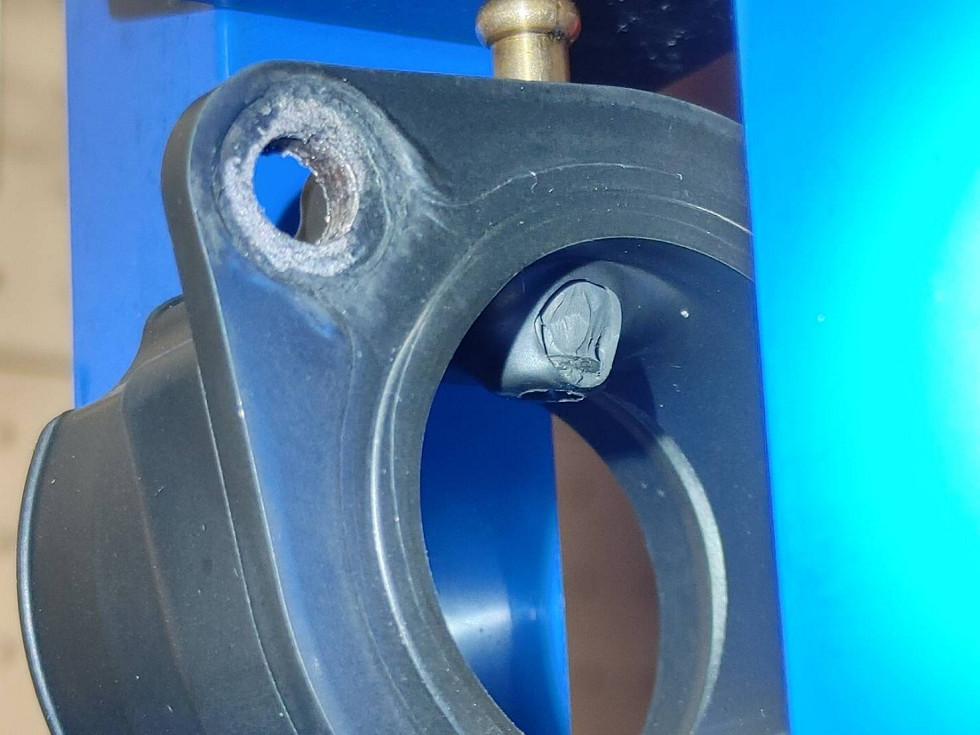
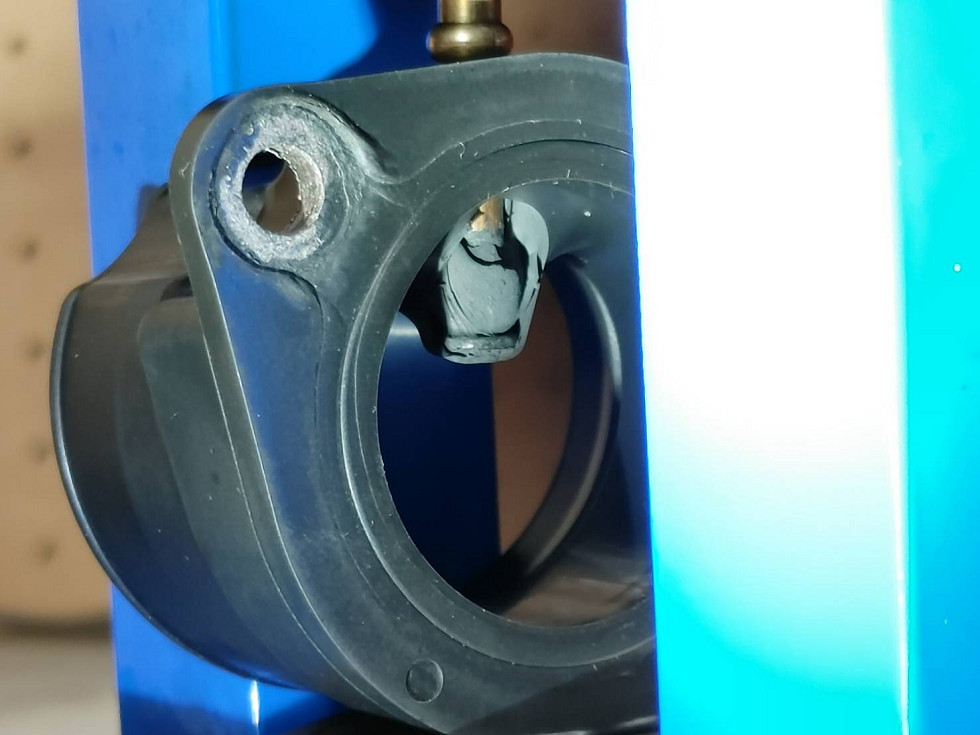
荷重を抜いてテスターから取り外したところ。
裂けてはいますが、分断はしていない事がわかります。
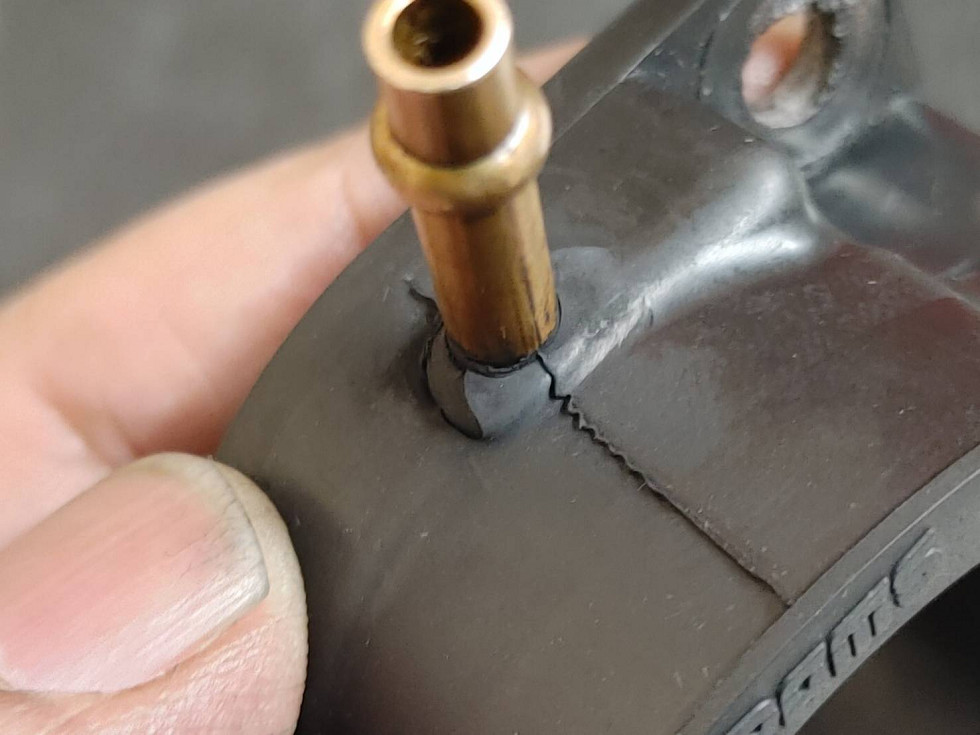
この状態で引っ張っても、指の力では千切る事が出来ません。
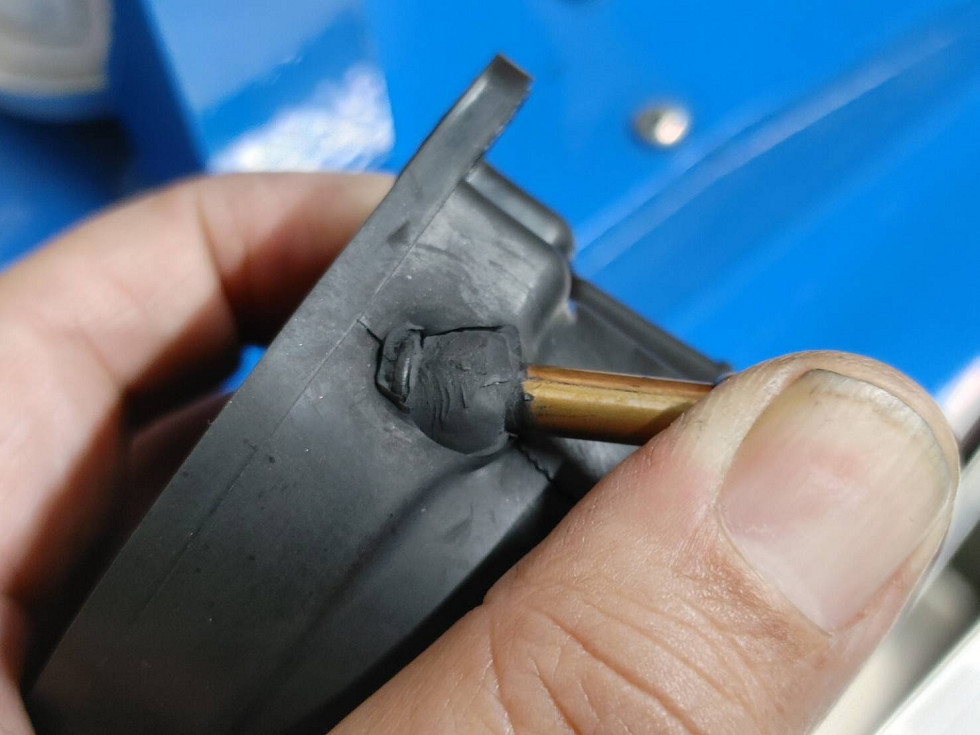
写真からわかりますが、パイプそのものに焼き付けられたゴムは剥がれてはいません。 その周囲のゴムの方が先に限界が来て裂けているのがわかるでしょう。
内面部にも裂けは発生していますが、パイプ周囲のゴムは半分近くが繋がっています。
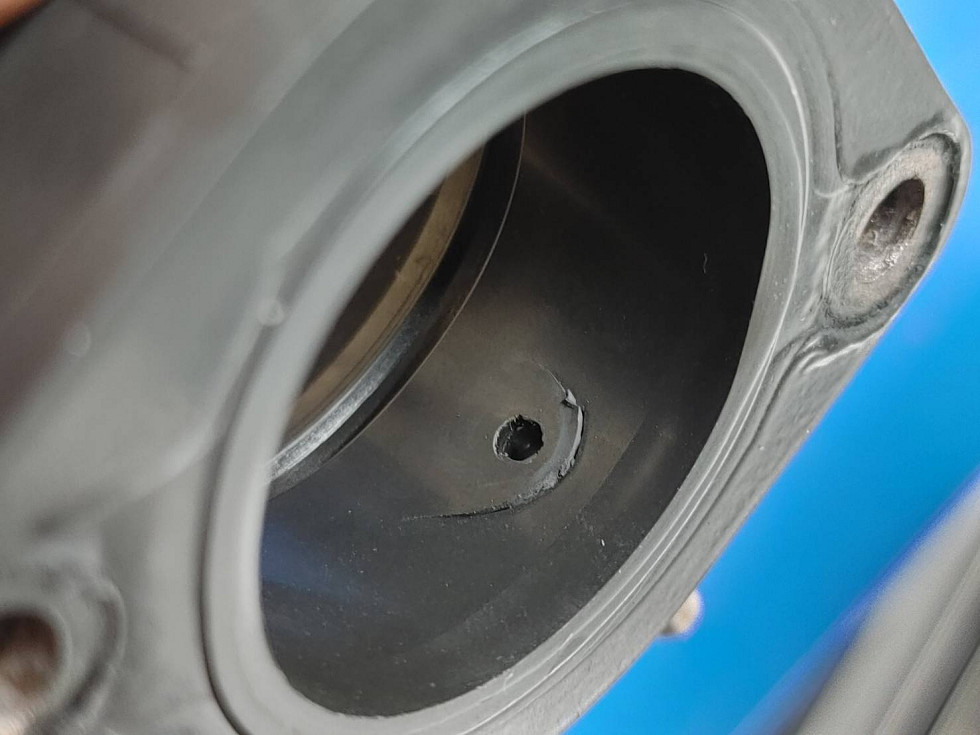
パイプの接着強度を知る為のテストでしたが、接着部が剥がれる以前にゴム部分が裂けてしまいました。
ゴム部分の強度についての測定となりましたが、このインシュレーターに使用さていているゴムは、厚さが10mm程度あると直径10mm以下の部分に集中して60㎏程度の荷重をかけないと裂く事が出来ないレベルの強度と弾性がある事になります。
社外キャブレターを使用する場合、エアクリーナーボックスからのダクトで反対側から支える事が無く、その重さをインシュレーター側のみで支える事が多いので負荷は増えるのですが、バンドによる締め付けトルクを上げられる様に薄く出来るのは、純正インシュレーターに比較してもこのゴム強度と耐ガス性が高い為です。
ちなみに、耐ガス性や耐熱性能にのみ関して言えばフッ素ゴム系のバイトンやシリコン等の方が優れてはいるのですが、バイトンは荷重に対する永久変型特性で、シリコン系は機械的な強度面で今回使用しているニトリル系等に共に劣る為、加硫成型してインシュレーターに使用するには向いていません。
(4輪等のインマニ配管に使用されるシリコンパイプには、必ず合成繊維の補強芯材を入れて強度を保つ様にされています。)