HPトップアイドラーを製作する際には、2種のフレームをスチール板の曲げ加工を行っています。
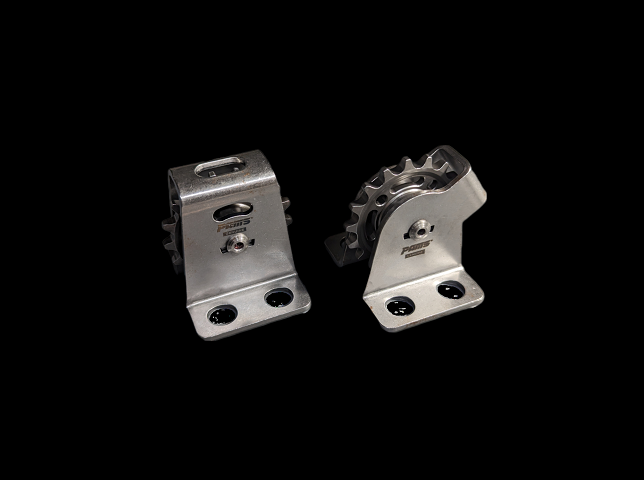
拘りましたのは、そのフレーム製作する際の曲げ手法と精度です。
さて、DIYで鉄板を鋭角に曲げる場合、内側にクサビを押し当てる様な手法で加工する方法があります。
例えばタガネとハンマーで鉄板を曲げる様な動画を見た事がある方は多いのでは無いでしょうか?
実は機械を使って少量の曲げ加工を行う場合にも、寸法を出し易い為に同様の手法で行われる場合はあります。
その場合の仕上がりはこの様になります。
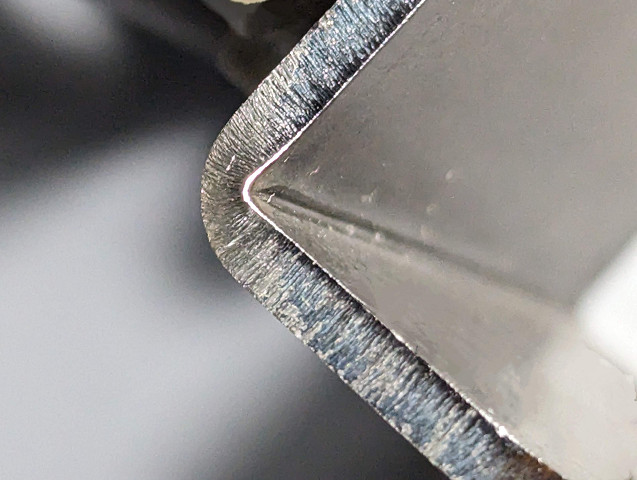
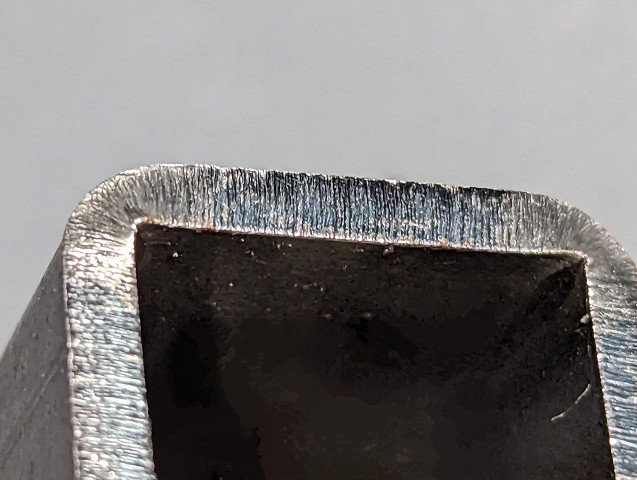
曲げ部分が外に向かって2/3程度に薄くなっているのがわかりますでしょうか
この手法は局部的に内側の角が潰れ、更に外側は引き延ばされて疲労が集中する上に薄くなり、¹極端に弱くなります。
その為、乗用車の外装の様にそれ自体には負荷のかからない薄板であればまだしも、何かを支え、高負荷や振動の多い場所に使う部品にはこの加工方法は使えません。
例えばZやJ系に限らず、フレームパーツでこの様に内側にエッジが食い込む様な曲げ方で製作されている場所は一箇所も無く、それがステムやピボット等の構造上の支点のみならず外装を装着するステーにおいてでもです。
フレームですらそうなのですから、エンジン內部のカムチェーンを支える部品をこの曲げ方をすると長年走っている内に曲げ部分にクラックが発生し、アイドラーごと上部が割れ飛んで大事になる可能性が非常に高くなります。
この為、弊社のアイドラーマウントフレームは専用に曲げ型を製作し、曲げ部の前後5mm以上の部分から緩やかに力を分散させる様にしています。
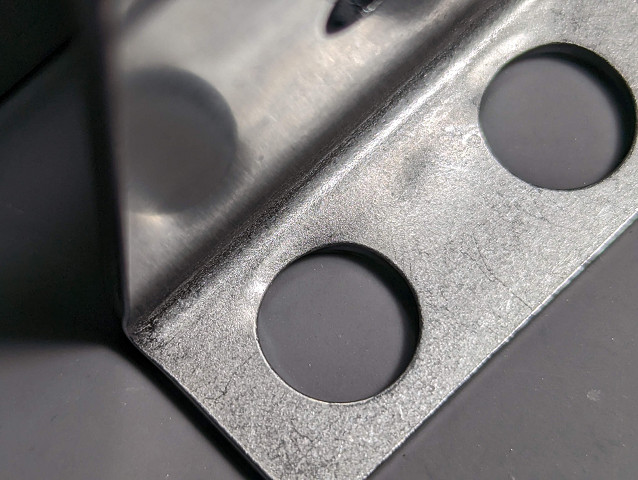
曲げ部は潰れず、変に薄くもなっていない事がわかります。
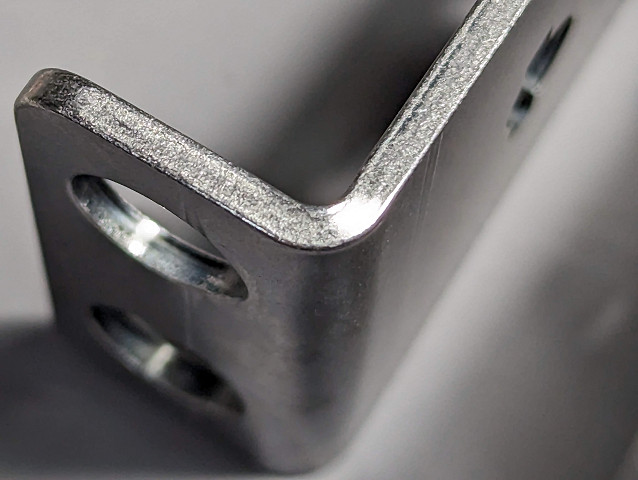
ちなみに、大きさの割に厚手の鉄板を、外形寸法やアイドラーを支える軸穴の位置を完全に均等な高さにしながら無理無く曲げるのは技術的難易度が高くなるのですが、専用の金型と治具により精度と耐久性の両方を実現する事が出来ました。
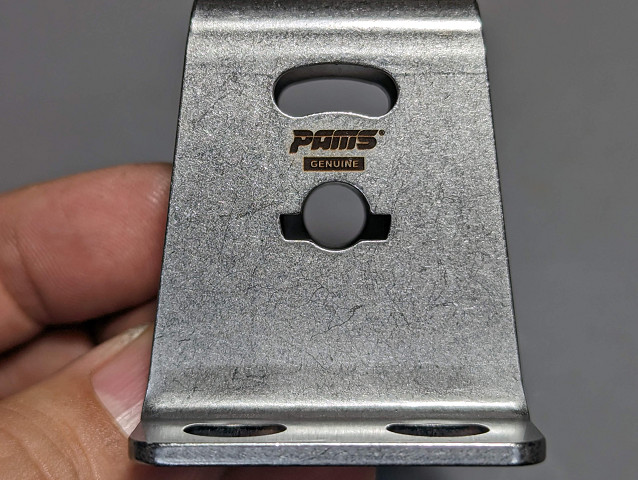
この様に穴の左右位置が完全に合っています。この精度が悪いと、高速で回転するアイドラーの軸が傾く為、大きなフリクションになります。
更に、更に応力集中による万が一の割れ可能性も下げる為に、断面や表面を全体的に研磨してきっかけとなるエッジを落としてあります。
HPトップアイドラーのフレームに指を強く当ててスライドしても指を切る様な事が無いレベルに仕上がっているのは、実は美観の為ではなく耐久性の為です。
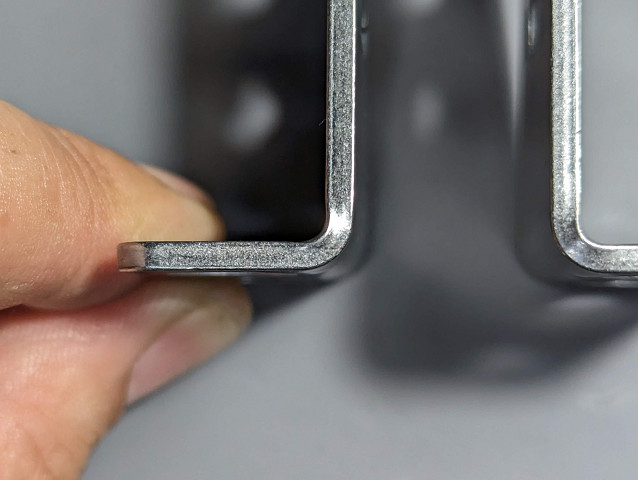